Mikro-Formguss im Detail
- Dominykas Turčinskas
- 9. März 2022
- 8 Min. Lesezeit
Aktualisiert: 19. Aug. 2022
Die Nachfrage nach Kunststoff-Mikro-Formguss steigt kontinuierlich. Der Grund: moderne Elektronikgeräte werden kontinuierlich kleiner und kompakter. Tauchen Sie mit Hilfe dieses Artikels ein in die neue Welt des Mikro-Spritzgusses! Erfahren Sie, wie Sie fertigungsgerecht entwerfen, Formmerkmale analysieren, das geeignete Material aussuchen …und was die Zukunft für den Mikro-Formguss parat hat!
Inhaltsverzeichnis:
„Was genau ist Mikro-Formguss, und worin zeichnet er sich aus?“
„Lässt sich Mikro-Spritzguss anstelle von herkömmlichem Spritzguss verwenden?“
„Wie breit ist das Einsatzspektrum von Mikro-Spritzguss branchenübergreifend?“
„Welche Materialien eignen sich am besten für den Mikro-Formguss?“
Herausforderungen des Mikro-Formgusses: Mikro-Montage und Micro-Packaging
Was genau ist Mikro-Formguss, und worin zeichnet er sich aus?
Mikrostrukturierte Aluminium- oder Stahlgussformen, die mit maximalen Toleranzen im Mikrometer- oder Submikrometerbereich CNC- und EDM-gearbeitet worden sind, stellen das Hauptmerkmal des Mikro-Formgusses dar. Das fertige Gussteil weist dann i.d.R. ein Gewicht von einem Bruchteil eines Gramms und/oder Mikrodetails von 50 µm bis hinab zu 5 µm Größe auf (oder sogar noch weniger).
Von herkömmlichen Formgussverfahren unterscheidet sich der Mikro-Formguss hauptsächlich in der Schussgröße und im Präzisionsgrad der Spritzanlagen. Da Mikro-Formgussanlagen über hochauflösendere Zufuhroptionen verfügen, die eine gleichmäßigere Druckverteilung innerhalb des Hohlraums zur Folge haben, ist es möglich, mit hoher Präzision Bruchteile eines Gramms einzuspritzen. Auch kommen hier insgesamt kleinere Gussformen zum Einsatz: Mikro-Gussformen sind mit kleineren Hohlräumen wie Kernstücken ausgestattet. Mikrostrukturen im Innern werden mittels hochpräziser CNC- und EDM-Maschinen gearbeitet. Aufgrund der Winzigkeit der fertigen Gussteile lassen sich hier – anders als beim herkömmlichen Formguss – die Bereiche Packaging und Qualitätsmanagement nicht als sekundäre Verfahren betrachten. Stattdessen verlangt beides ein hohes Maß an Aufmerksamkeit in den Einzelheiten.
Lässt sich Mikro-Spritzguss anstelle von herkömmlichem Spritzguss einsetzen?
Auf den Punkt gebracht: Ja! Nicht immer ist Mikro-Formguss notwendigerweise ‚mikro‘. Es gibt eine Vielzahl an Anwendungsfällen, in denen auch herkömmliche Kunststoffkleinteile innerhalb der typischen Mikro-Formgussdimensionen und des Mikro-Einspritzvolumens liegen – also etwa innerhalb ⌀~100 mm Kugeldurchmesser bzw. ~15-30 cm³ Volumen. Ein relativ neuer, innovativer Trend ist der Produkt-Schnupper-Launch in risikoarmer Kleinauflage von weniger als 100.000 Stück – ideal für den Einsatz von Mikro-Formguss.
In der Abbildung hier veranschaulicht ist der optimale Einsatzbereich des Mikro-Formgussverfahrens. Innerhalb dieses Bereichs sind gegenüber dem herkömmlichen Spritzguss erhebliche Zeit- und Kostenersparnisse möglich. Die Tooling-Kosten lassen sich gar um den Faktor 3-4× senken, und vom ersten Entwurf bis zur Markteinführung dauert es mitunter gerade einmal 3 Wochen.
Geringe Anlagenbetriebskosten, dank kleinerer Anlagengrößen bei geringerer Klemmkraftanforderung
Schnellere, günstigere Maschinenbearbeitung aufgrund weniger Gussformhohlräume und geringeren Aluminiumverbrauchs
Kürzere Gusskanäle bedeuten weniger Ausschuss.
Ein weiterer positiver Effekt der weitaus schnelleren und günstigeren Gussformfertigung ist ein Gewinn an Flexibilität beim Vornehmen kurzfristiger Änderungen.

Wie breit ist das Einsatzspektrum von Mikro-Spritzguss branchenübergreifend?
In Medizin und Gesundheitswesen
Gerade der medizinische Einsatz erfordert häufig ein hohes Maß an Präzision. Oft geht dies mit filigranen Einzelteilen von geringer Größe einher. Entsprechend sind medizinische Anwendungen eines der Haupteinsatzgebiete des Mikro-Formgusses – von Dosierungshilfen, Diagnosehilfsmitteln, über Seh- und Hörhilfen, bis hin zu minimal-invasiven OP-Instrumenten, Kathetern etc.
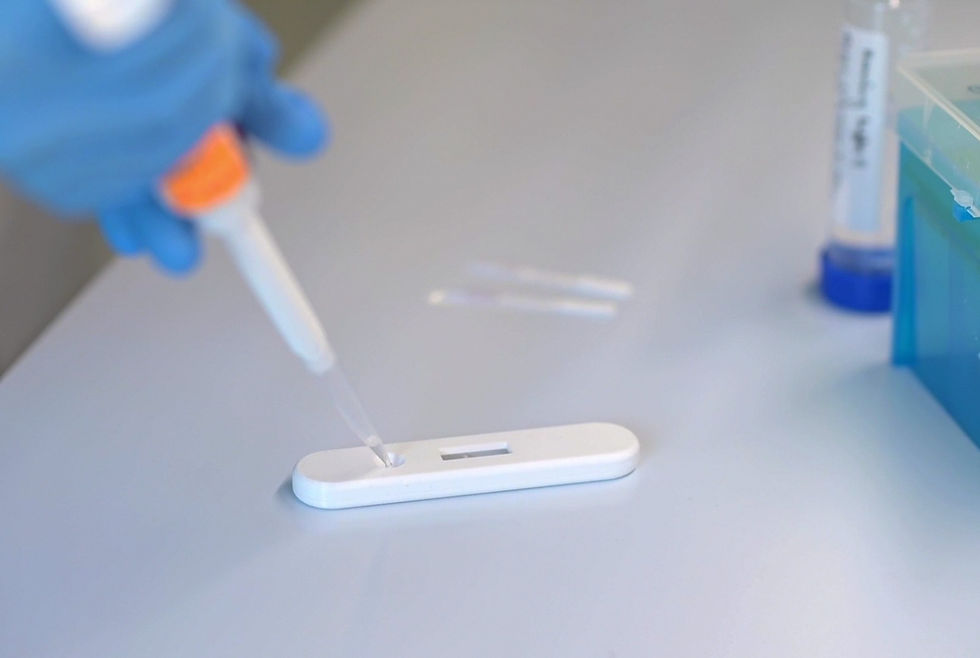
Mikrofluidsysteme stellen einen neuen Trend dar, der in einem breiten Spektrum medizinischer Anwendungen (einschließlich Point-Of-Care-Diagnostik) zunehmend an Bedeutung gewinnt. Dass die Medizinbranche gut ein Viertel des weltweiten Marktanteils des Mikro-Spritzgusses stellt, dürfte an dieser Stelle kaum überraschen (Quelle: 'Mordor Intelligence').
In der Elektronikbranche
Da moderne Unterhaltungs- und Kommunikations-elektronik weiterhin immer kleiner und kompakter wird, wächst auch hier der Bedarf an immer kleineren und filigraneren Kunststoffteilen ungebrochen – und somit auch der Einsatzbereich des Mikro-Formgusses mit seinen spezifischen Vorteilen. Ein prägnantes Beispiel ist hier das Feld der Mikro-Optik, beispielsweise in Form von Laser-Linsen, Smartphone-Kameras, Virtual-Reality-Hardware usw. Daneben eher traditionelle Mikroelektronik wie Stecker, Schalter, Tasten, Platinenbauteile – für Laptops, Telekommunikationsanlagen, Multimedia und vieles mehr.

Ein weiteres Einsatzgebiet für den Mikro-Formguss stellen Mikroelektromechanische Systeme (MEMS) dar. Diese Sparte befindet sich in einer steilen Wachstumsphase, was sich entsprechend positiv auf die Nachfrage nach den innovativen Verfahren des Mikro-Formgusses auswirkt. Eine Schnittstelle zum medizinischen Bereich stellen BioMEMS (Biomedizinische MEMS) dar, die zunehmend für den Einsatz im Next Generation Sequencing (NGS) und zur Point-of-Care-Diagnostik herangezogen werden.
Der technische Fortschritt in der Elektronikbranche galoppiert weiterhin, und so überrascht es kaum, dass mehr als ein Fünftel des weltweiten Mikro-Spritzguss-Marktanteils genau hier zu verorten sind (ebenda).
In der Automobilbranche

Moderne PKWs und LKWs enthalten ebenso mehr und mehr kleine, filigrane und ultrakompakte Kunststoffbauteile. Da wären einerseits die unzähligen Klammern, Unterlegscheiben, Türschlossmechanismus-Bauteile, Tasten, Knöpfe, Zahnrädchen und mehr, aber auch Motor- und Bremssystemkomponenten etc. „unter der Haube“. In Anbetracht der schieren Größe der Automobilindustrie und der schieren Anzahl an Einzelteilen, die in jedem einzelnen Kraftfahrzeug stecken, ist es kaum ein Wunder, dass der Sektor knapp ein Drittel des weltweiten Mikro-Formgussbedarfs ausmacht (ebenda).
Wo liegen die Limits des Dünnwand-Formgusses?
Um das Thema Dünnwand-Formguss zu beleuchten, sollten wir uns zunächst Klarheit über das Grundkonzept des Verfahrens verschaffen. Das Verhältnis zwischen Fließweg und Wanddicke – L/t – ist ausschlaggebend. Darin unterscheiden sich die diversen Kunststoffe teils erheblich. Hier das maximale L/t-Verhältnis der zehn am häufigsten eingesetzten Thermoplasten:
ABS: 170/1
SAN: 120/1
PA: 150/1
PC: 100/1
HDPE: 225/1
LDPE: 275/1
PP: 250/1
PMMA: 130/1
POM: 150/1
PS: 200/1
Das korrekte Festlegen der Wanddicke ist wesentlich verantwortlich für das Qualitätsniveau des resultierenden Gussteils. Für den entwerfenden Ingenieur bedeutet dies, sorgsam Materialwahl und Wanddicken aneinander anzupassen und die Seitenverhältnisse durch den gesamten Entwurfsprozess hindurch zu harmonisieren. Zu den möglichen Folgen in der Fertigungsphase aus einer unzureichenden Berücksichtigung dieser Punkte zählen unter Anderem:
Verlängerte Durchlaufzeiten, da das Abkühlen dickerer Wände mehr Zeit beansprucht
Zu dünne Wände sind evtl. zu instabil und können überdies Probleme mit der Flussrate (das Flusstempo des Kunststoffs in die Hohlräume hinein) hervorrufen. Gusslücken können entstehen, falls das Material die betreffenden Stellen nicht erreicht, bevor es bereits zu erstarren begonnen hat.
Ungleichmäßige Wanddicken haben unterschiedliche Abkühl- bzw. Aushärtungsdauern zur Folge, was häufig ein wesentlicher Faktor in der Entstehung von Einfallstellen und Verwölbungen am fertigen Gussteil ist.
Da der Dünnwand-Formguss vor allem von der richtigen Materialwahl abhängt, ist es ratsam, empirische Daten heranzuziehen. Die am häufigsten eingesetzten Kunststoffe samt ihrer jeweiligen für den Spritzguss empfohlenen Mindest- und Höchstwanddicken sind in der folgenden Tabelle verzeichnet:
MATERIAL | ANWENDUNG | WANDDICKE |
ABS | Hauptsächlich Automobil- und Sanitäranlagenbau | 0,143 mm - 3,556 mm |
AZETAL | Mitunter Ersatz für Komponenten, die zuvor aus | 0,762 mm - 3,048 mm |
AKRYL | Metall waren Hauptsächlich anstelle von Glas in | 0,635 mm - 12,70 mm |
NYLON (POLYAMID) | Diverse industrielle/mechanische Anwendungen | 0,762 mm - 2,921 mm |
POLYKARBONAT | Einsatz in einem breiten Spektrum von Branchen | 1,016 mm - 3,810 mm |
POLYESTER | Einsatz in einem breiten Spektrum von Branchen | 0,635 mm - 3,175 mm |
POLYETHYLEN | Ideal für Einweg- und Mehrwegverpackungen/- | 0,762 mm - 5,080 mm |
POLYPROPYLEN | produkte Dank seiner Lebensmittelechtheit hauptsächlich im Nahrungsmittelbereich | 0,635 mm - 3,810 mm |
POLYSTYREN | Einsatz in einem breiten Spektrum von Branchen | 0,889 mm - 3,810 mm |
POLYURETHAN
| Einsatz in einem breiten Spektrum von Branchen | 2,032 mm - 19,05 mm |
Bei der Wahl des geeigneten Rohmaterials sind einige weitere Anforderungen an den Dünnwand-Formguss zu berücksichtigen. Da dünne Wände schneller abkühlen als dicke, erfordert der Dünnwand-Formguss ein höheres Hohlraumfülltempo. Beispielsweise erfordern um 25% dünnere Wände eine um 50% reduzierte Hohlraumfülldauer bzw. ein entsprechend höheres Tempo. Um das höhere Tempo und den höheren Druck zu erzielen, macht der Dünnwand-Formguss spezielle Anlagen erforderlich – auch wenn dies im Zuge des technologischen Fortschritts immer dünnere Wände betrifft, die ansonsten zunehmend auch mit Standard-Formgussanlagen realisierbar sind.
Welche Materialien eignen sich am besten für den Mikro-Formguss?

Zwar kommt für den Mikro-Formguss eine ganze Bandbreite an Rohmaterialien in Frage, doch gibt es definitiv ein paar entscheidende Einschränkungen, die bei der Materialwahl zu berücksichtigen sind – wie etwa die mechanischen Eigenschaften betreffs der Anwendungsumgebung inkl. Umgebungstemperatur und/oder Feuchtigkeit, die biologische Verträglichkeit, das Erscheinungsbild sowie natürlich der Preis. In der untenstehenden Tabelle wieder eine Auswahl der gängigsten Rohmaterialien für den Mikro-Formguss:
MATERIAL | MATERIAL |
LCP (Flüssigkristall-Polymer) | Hohe Temperaturunempfindlichkeit; hohe Chemikalien- und Wetterbeständigkeit; Spannungsrissbeständigkeit |
PMMA (Polymethylmethakrylat) | Hohe Transparenz; UV-Strahlungsresistenz; Kratzfestigkeit
|
COCs (Zyklische Olefin-Copolymere) PEEK (Polyetheretherketon) | Hohe Fließfähigkeit; Hitze-, Chemikalien- und Feuchtigkeitsbeständigkeit; hoher Klarheitsgrad |
Hohe Chemikalienbeständigkeit; hervorragende Hitze- und Drucktoleranz; Spannungsrissbeständigkeit und hohe Strapazierbarkeit | |
PLA (Poly-Milchsäure) | Biologische Resorbierbarkeit; hohe Transparenz; hohe Verträglichkeit |
PGA (Polyglykolidsäure) | Biologische Resorbierbarkeit; hohe Strapazierbarkeit; hohe Scheuer- und Lösungsmittelresistenz |
Polyethylen | |
Polypropylen | Hohe Chemikalienbeständigkeit; hohe Strapazierbarkeit und Oberflächenhärte; Abriebfestigkeit |
Polykarbonat
| Hohe Chemikalien- und Hitzebeständigkeit; hohe Biege- und Ermüdungsfestigkeit; elektrisch isolierend Hohe Transparenz und Formstabilität; Rigidität und Zähigkeit; Feuchtigkeits- und Chemikalienbeständigkeit |
Eine der wichtigsten Wachstumssparten des Mikro-Spritzgusses stellt der Einsatz bioresorbierbarer Polymere dar – naheliegenderweise insbesondere im medizinischen Bereich. Dank dieser Polymere lässt sich die Anzahl operativer Eingriffe reduzieren, da temporäre Implantate mit der Zeit vom menschlichen Körper resorbiert, also auf natürliche Weise abgebaut werden. Ein nachträgliches operatives Entfernen ist somit nicht mehr nötig. Nicht zuletzt aufgrund von Innovationen wie dieser steht der Mikro-Formguss hoch im Kurs!
Was hält die Zukunft für den Mikro-Spritzguss parat?
In fast jeder fertigenden Branche weltweit kommt heute der Kunststoff-Spritzguss zum Einsatz. Im Zuge der industriellen Revolution 4.0 ersetzen in rasantem Tempo immer mehr neue, optimiertere und nachhaltigere Fertigungsverfahren das Althergebrachte. So auch der Mikro-Formguss, der die wachsende Nachfrage nach immer kleineren, kompakteren und filigraneren Kunststoffbauteilen bedient. Doch auch der Mikro-Formguss ruht sich nicht auf seinen Lorbeeren aus! Hier einige aktuelle Trends & Innovationen aus dem Bereich:
Signifikante Verbesserungen im Schadstoff-Management. Das zunehmende Umweltbewusstsein der Gesellschaft motiviert Unternehmen zur Erforschung neuer, verbesserter Kunststofffertigungs- und -Recycling-Verfahren.
Die treibende Kraft für Innovationen schlechthin ist natürlich weiterhin die Nachfrage: Immer wieder wenden sich fertigende Unternehmen mit neuen Wünschen an die Spritzguss-Branche, was neue Herausforderungen stellt. Beispielsweise Extrem-Dünnwand-Formguss oder der automatisierte Insert-Formguss – beides Neuerungen in direkter Folge von Kundennachfrage.
Neue, verkleinerte Sensoren lassen sich direkt in die Mikro-Gussformen einpassen, wofür die Sensoren der älteren Generation noch nicht klein genug waren. Zusätzlich sind die neuen, ultrakompakten Sensoren leichter zu installieren. Sie dienen u.a. der Kontrolle von Temperatur und Druck sowie dem Erkennen von Verziehungen, Verschrumpfungen etc.
Neueste Innovationen finden sich im Bereich CNC-Tools und Mikro-Sinker-EDM. Sie gestatten Spritzgießern hochpräzise Schüsse von weniger als 1 Gramm Gewicht. Fortschritte in Sachen Sensor-Hardware ermöglichen eine noch genauere Überwachung und Steuerung der Prozesse in Echtzeit.

Dank neuer, angussloser Gussformen bzw. Gussformen mit reduzierten Kanallängen lässt sich viel Material sparen, was wiederum Anlagenkonstrukteuren den Entwurf noch präziserer Anlagen bei noch kleineren Schussgrößen ermöglicht. Weitere Fortschritte beinhalten Entwürfe auf Basis von Non-Standard-Materialien, verbesserte Dünnwand-Füllverfahren, Gussformtempern zwecks Entfernen von Materialspannung sowie verbesserte Gussform- und Material-Monitoringsysteme.
Herausforderungen des Mikro-Formgusses: Mikro-Montage und Micro-Packaging
Ein wesentlicher Kostenfaktor speziell bei Produkten im Mikro-Maßstab sind die Mikro-Montage- und Packaging-Kosten – somit ein zentraler Punkt, der bei der Entwicklung von Mikro-Produkten zu berücksichtigen ist, und ein wesentlicher Schlüssel zum Markterfolg neuer Produkte.
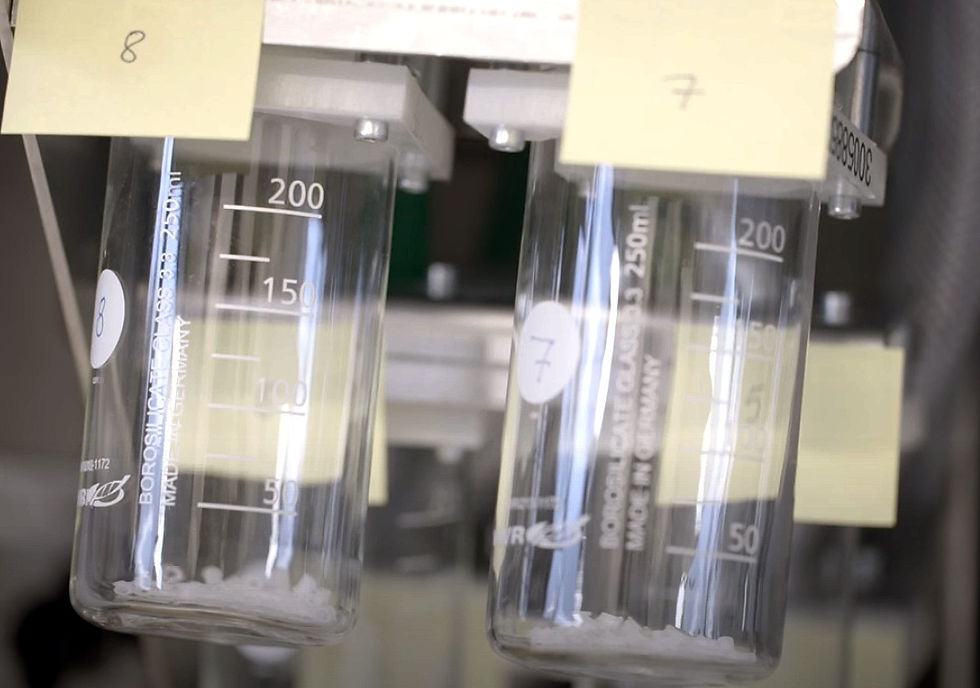
Dass die Kosten von Montage und Packaging gerade bei Produkten im Mikro-Maßstab so stark ins Gewicht fallen, liegt allem voran an der bislang geringen Automatisierung der beiden Prozesse in diesem Bereich: Die Montage erfolgt i.d.R. von Menschenhand, mittels Mikroskop und Mikropinzette. Die dazu erforderlichen Fachkräfte wollen bezahlt werden, und somit schießen die Kosten in die Höhe. Überdies ist der Zeitaufwand größer, und die Fachkräfte leiden oft an Müdigkeit der Augen und Verspannungen des Nackens etc. Die Qualitätsanforderungen an ihre Arbeit sind enorm.
Jedoch gibt es auch neues Arbeitsequipment in Form spezieller Werkzeuge, die das Vorgehen erleichtern:
Optische Systeme, die mit besonders leistungsfähigen Stereo-Mikroskopen samt hochauflösenden Kameras und Bildschirmen ausgestattet sind. Letztere zeigen in Echtzeit Instruktionen und nützliches Feedback an, was die Arbeit zusätzlich leichter und effizienter macht.
Mikro-Stellungsregler mit 40 nm Auflösung sowie entsprechende Mikrogreifer und Positionsmanagement-Software für ein bisher unerreichtes Maß an intuitiver Kontrolle und Genauigkeit.
Echtzeit-Computervision zur Steuerung von Servo-Motoren im Mikrometerbereich.

Hochauflösende Präzisionsübertragungswerkzeuge zum Handhaben und Weiterleiten der Werkstücke und Komponenten.
Aber auch falls Sie für Ihr Mikro-Produkt die Montage unterm Mikroskop ganz umgehen möchten, stehen Ihnen einige Verfahren zur Verfügung, um unterschiedliche Einzelteile bereits im Entwurfsstadium zu kombinieren:
Doppelschuss-Mikro-Formguss, der es gestattet, in eine Gussform zwei unterschiedliche Materialien einzuspritzen – ob an derselben Stelle oder an unterschiedlichen Stellen der Gussform
Ultraschallschweißen zum Verbinden der Thermoplaste mit geeigneten Metallteilen
Laser-Schweißen kommt vor allem dann zum Einsatz, wenn sich die räumliche Geometrie nicht mittels Over-Molding kombinieren lässt. Ebenso lässt sich das Laser-Schweißen dazu verwenden, um Materialien wieder sauber zu trennen – wie etwa Drähte.
Das Heißverstemmen ist eine überaus preisgünstige Art, Polymere und Metall durch Verschränken der Materialien miteinander zu verbinden
Das Verfahren des Lösemittel-Verbackens ist als eine der preisgünstigeren wie schnelleren Methoden zum Verbinden von Komponenten im Mikro-Maßstab bekannt – vor allem bei der Fertigung von Implantaten. Dazu kommen Mikro- und Nanopipetten zum Einsatz.
Kaum weniger wichtig als die Mikro-Montage ist das Verpacken der Mikro-Komponenten, denn nur so kommen die filigranen Gussteile sicher und wohlbehalten beim Kunden an. Der Versand von besonders kleinen, filigranen, stoß- und/oder gar vibrationsempfindlichen Teilen stellt hohe Anforderungen an die Verpackung und erfordert somit ein hohes Maß an Sorgfalt schon in der Planung. In aller Regel bedeutet dies Einzelverpackungen. Beim Versand von Reinraum zu Reinraum spielt oft die Einhaltung der ISO 13485-Norm eine zentrale Rolle, was u.a. das Sicherstellen der geeigneten Umgebungstemperatur und Umlüftung durch luftgefilterte Ventilationssysteme erfordert, um auch den letzten Staubpartikel daran zu hindern, sich auf dem bloßen Mikro-Gussteil niederzulassen.
Inhaltsverzeichnis:
„Was genau ist Mikro-Formguss, und worin zeichnet er sich aus?“
„Lässt sich Mikro-Spritzguss anstelle von herkömmlichem Spritzguss verwenden?“
„Wie breit ist das Einsatzspektrum von Mikro-Spritzguss branchenübergreifend?“
Mikro-Formguss in der Medizin
Mikro-Formguss in Elektronikprodukten
Mikro-Formguss im Automobilbau
„Wo liegen die Limits des Dünnwand-Formgusses?“
„Welche Materialien eignen sich am besten für den Mikro-Formguss?“
„Was hält die Zukunft für den Mikro-Spritzguss parat?“
Herausforderungen des Mikro-Formgusses: Mikro-Montage und Micro-Packaging
Comments