MFI Medizinische Industrie verwendet Mikroformen für Elektrodengehäuse aus Kunststoff
- Dominykas Turčinskas
- 6. Apr. 2022
- 3 Min. Lesezeit
Aktualisiert: 22. Aug. 2022
MFI (medizinisch, industriell) bietet Design-, Konstruktions- und Produktionsdienstleistungen in den Bereichen Medizin und Industrie für hochwertige, auf Anfrage gefertigte Kabel und Drähte. Das Unternehmen ist spezialisiert auf kundenspezifische Kabelbäume, Montage von Steckern, EEG-Kappen, Kabeldesign, Löten von Feindrähten und vieles mehr.
MFI ist ein Unternehmen, das über 15 Jahre Erfahrung im medizinischen und industriellen Bereich verfügt. MFI hat sich einen Namen in der Herstellung von kundenspezifischen Drähten, Elektroden und ähnlichen Produktkategorien gemacht. MFI verfügt über ein engagiertes Team von Ingenieuren, die Experten in 3D-Modellierung, Maschinenbau, Prototyping und Fertigung sind. All dies dient der Schaffung einer zuverlässigen Verbindung für den Kunden.
Unterauftragsvergabe
Wenn es um die Vergabe von Unteraufträgen an andere Fertigungsunternehmen geht, ist man immer neugierig darauf, etwas Ähnliches zwischen den Partnern herauszufinden. Wir waren froh, als wir erfuhren, dass wir viele Gemeinsamkeiten mit der Kabelumspritzung haben - obwohl Micromolds sich auf die
Mikroumspritzungstechnologie spezialisiert hat, haben wir in der Vergangenheit auch einige Kabelumspritzungsprojekte durchgeführt. Vielleicht hat dieses verwandte Thema dazu beigetragen, eine stärkere Partnerschaft mit anderen zukünftigen Projekten zu entwickeln.
Erhalt einer RFQ
Bei dieser Zusammenarbeit ging es um das Spritzgießen eines Kunststoffgehäuses für die Elektrode. Als wir die Anfrage erhielten, war uns sofort klar, dass wir das ohne große Konkurrenz machen können, denn wir konnten alle unten aufgeführten Punkte ankreuzen:
- Das Teil war so klein, dass wir sogar 8 oder 16 Kavitäten in einer einzigen Mikroform herstellen konnten;
- Das Produktionsvolumen lag bei bis zu 100.000 Stück;
- Es wies einige Mikroeigenschaften auf, die nur mit der Mikroformtechnik erreicht werden konnten.
- Dringlichkeit - das Projekt musste in wenigen Wochen abgeschlossen sein und es
wurden schnelle Prototypen benötigt.
- Wir hatten ABS-Material in medizinischer Qualität auf Lager.
Das Produkt war ideal für unsere Mikrospritzgusstechnologie und wir waren uns sicher, dass wir dem Kunden ein wettbewerbsfähiges Angebot machen können.
DFM-Analyse und Optimierung der Teile für das Gießen

Nach der Auftragsbestätigung folgte, wie immer, die DFM. Da es sich bei dem Auftraggeber um einen Hersteller handelte, der selbst über ein ausgeprägtes Ingenieurwissen verfügte, war die Qualität des CAD-Modells hervorragend. Ebenso wie die erhaltene Anfrage selbst.
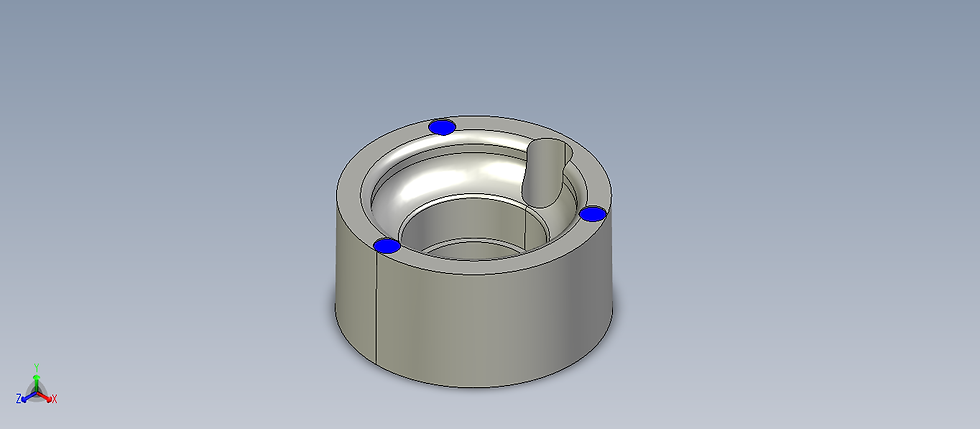
"Das nennen wir eine qualitative Anfrage, die sowohl dem Kunden als auch dem Hersteller hilft, Zeit zu sparen" - sagt Geschäftsführer Jonas
Wir mussten lediglich einige Entformungswinkel für einige Bereiche hinzufügen und uns auch auf Einspritzpunkte und Auswerfermarken einigen. Der Prozess verlief schnell und reibungslos, so dass wir in etwa 3 Tagen zum Werkzeugbau übergehen konnten.
Der Werkzeugbau - Formenbau
Wir verwendeten Aluminium-Mikroformen mit 4 Kavitäten. Eine EDM-Bearbeitung war nicht erforderlich. Wir hatten die Formen in weniger als 1 Woche für die Herstellung von Mustern fertig.

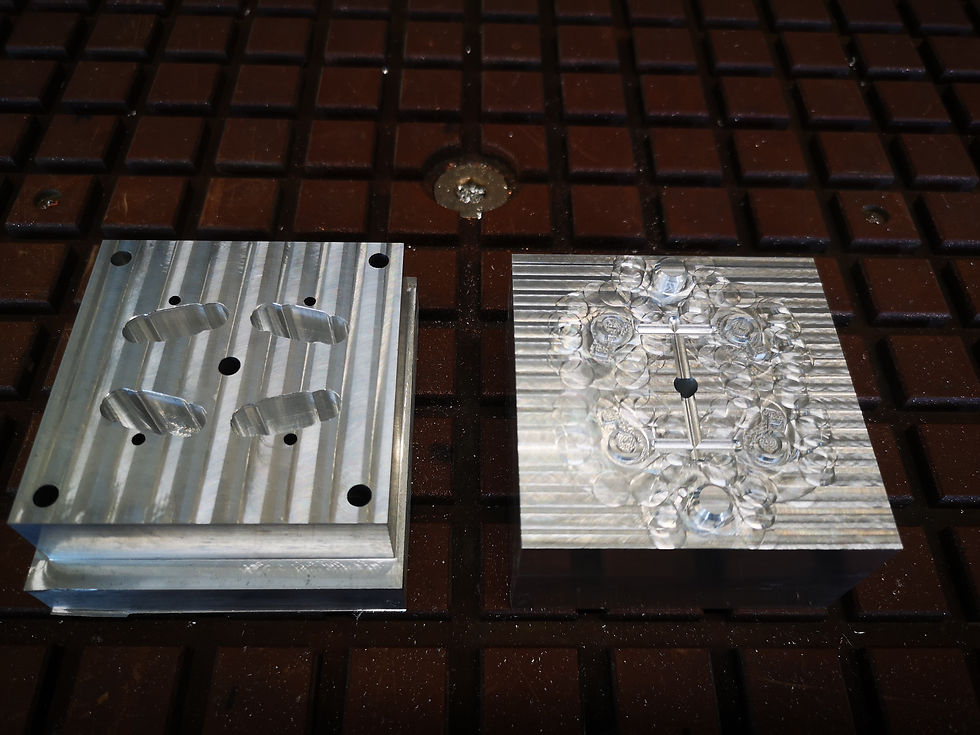
Musterprüfung T1
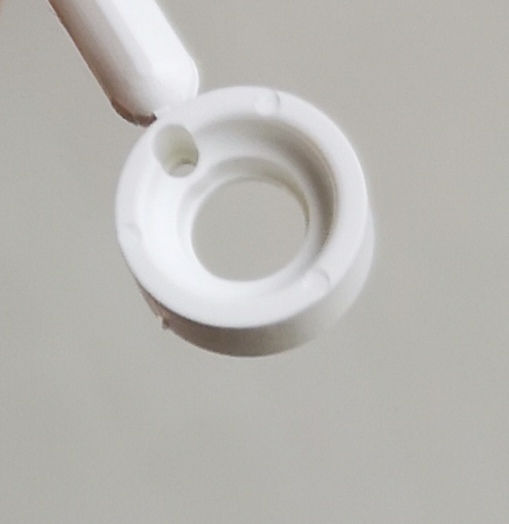
Wenn wir die Muster gießen, sind wir die ersten, die sie prüfen und die Qualität der geleisteten Arbeit beurteilen können. Wie immer sind wir ehrlich und transparent gegenüber dem Kunden und teilen bei Bedarf optische Bilder oder Videos der aufgetretenen Mängel mit.
Es gibt jedoch 2 Typen von Fehlern: Sie können durch den Gießer (uns) oder durch den Kunden verursacht werden - durch das Design des Teils. In diesem Fall, als wir die erste Rückmeldung erhielten, gab es gegensätzliche Meinungen: die gebrochene Wand könnte durch die falsche Position der Stricklinie (schlechte Optimierung des Teils - unsere Verantwortung) oder durch schlechtes Design (Verantwortung des Kunden) entstanden sein. Dank des Fachwissens sowohl der Ingenieure des Kunden als auch der unseren konnten wir uns darauf einigen, dass es sich nicht um eine Stricklinie handelte, die in dieser Situation nicht möglich war, wie auf dem Bild zu sehen.

Beide Parteien konnten sich darauf einigen, dass die Wand dicker werden sollte, und so war die Lösung der Herausforderung schnell gefunden. Wie Ronald de Vreeze, der Geschäftsführer von MFI, sagen würde:
"Wir haben für fast jede Herausforderung eine Lösung - ob es sich nun um Spezialanfertigungen in Einzelstücken oder Großserien handelt..."
Bei der Modifikation der Form können wir aufgrund der subtraktiven Art der CNC-Bearbeitung das Material nur aus der Form herausschneiden, aber nicht wieder hinzufügen. Da die Wand verdickt werden musste, war die Modifikation eine kleine Änderung, die wir in wenigen Tagen durchgeführt haben.
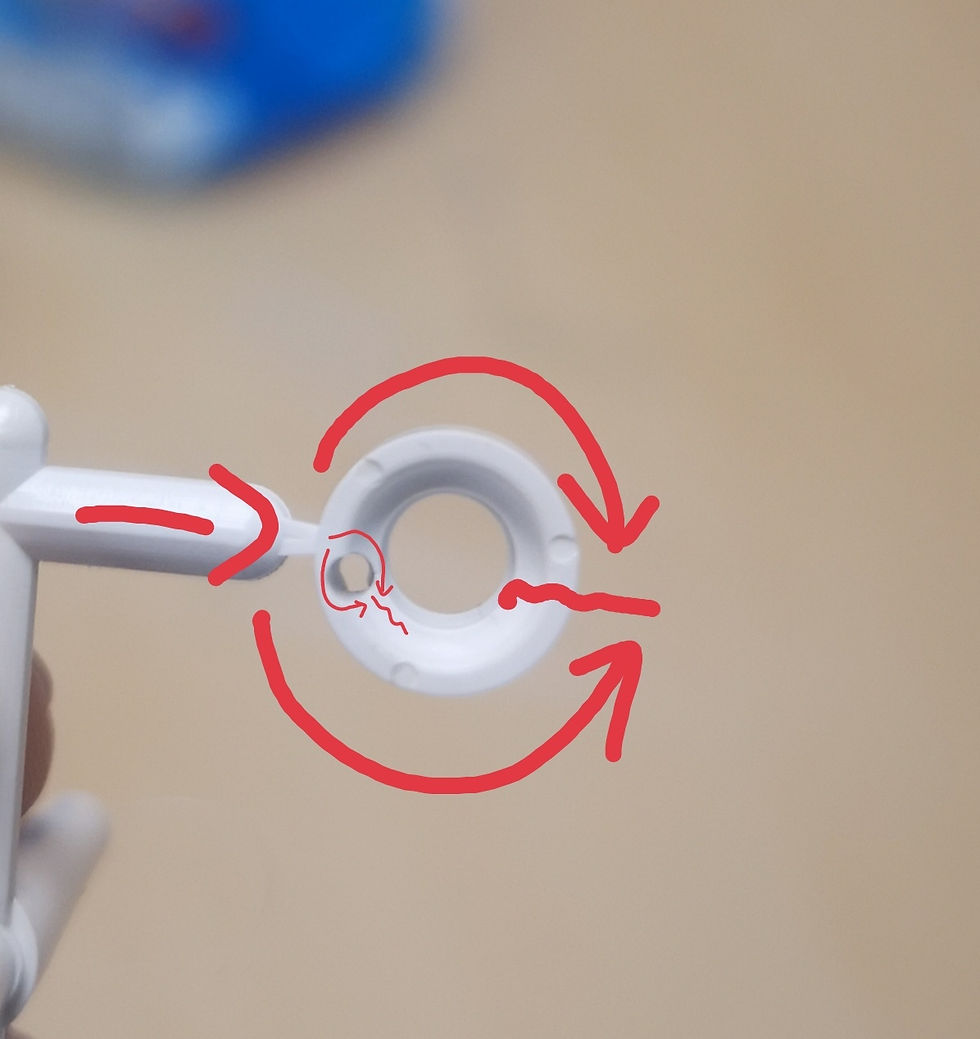
Abschluss
Da die Änderungen offensichtlich und geringfügig waren, beschloss der Kunde, auf die Musterprüfung T2 zu verzichten, und wir gingen direkt zur Herstellung der ersten Charge über. Obwohl wir nach dem Versand der ersten Charge etwas nervös waren, erhielten wir einen weiteren Auftrag für Charge 2, und die Nervosität verflog sofort, da die Ergebnisse zufriedenstellend waren.

Wir waren nicht nur bei diesem einen Projekt erfolgreich, sondern haben auch eine starke Partnerschaft mit einem MFI-Unternehmen aufgebaut - die nächsten zwei Projekte stehen an, und wir nehmen dies als Beweis dafür, dass wir wirklich gute Arbeit gemacht haben.
Comments